May, 2022: Muting'ong'o Community Spring Protection Complete!
Muting'ong'o Community now has access to clean water! We transformed Lukasile Burudi Spring into a flowing source of naturally filtered water thanks to your donation. Our team also trained the community on improved sanitation and hygiene practices. Together, these components will unlock the opportunity for community members to live better, healthier lives.
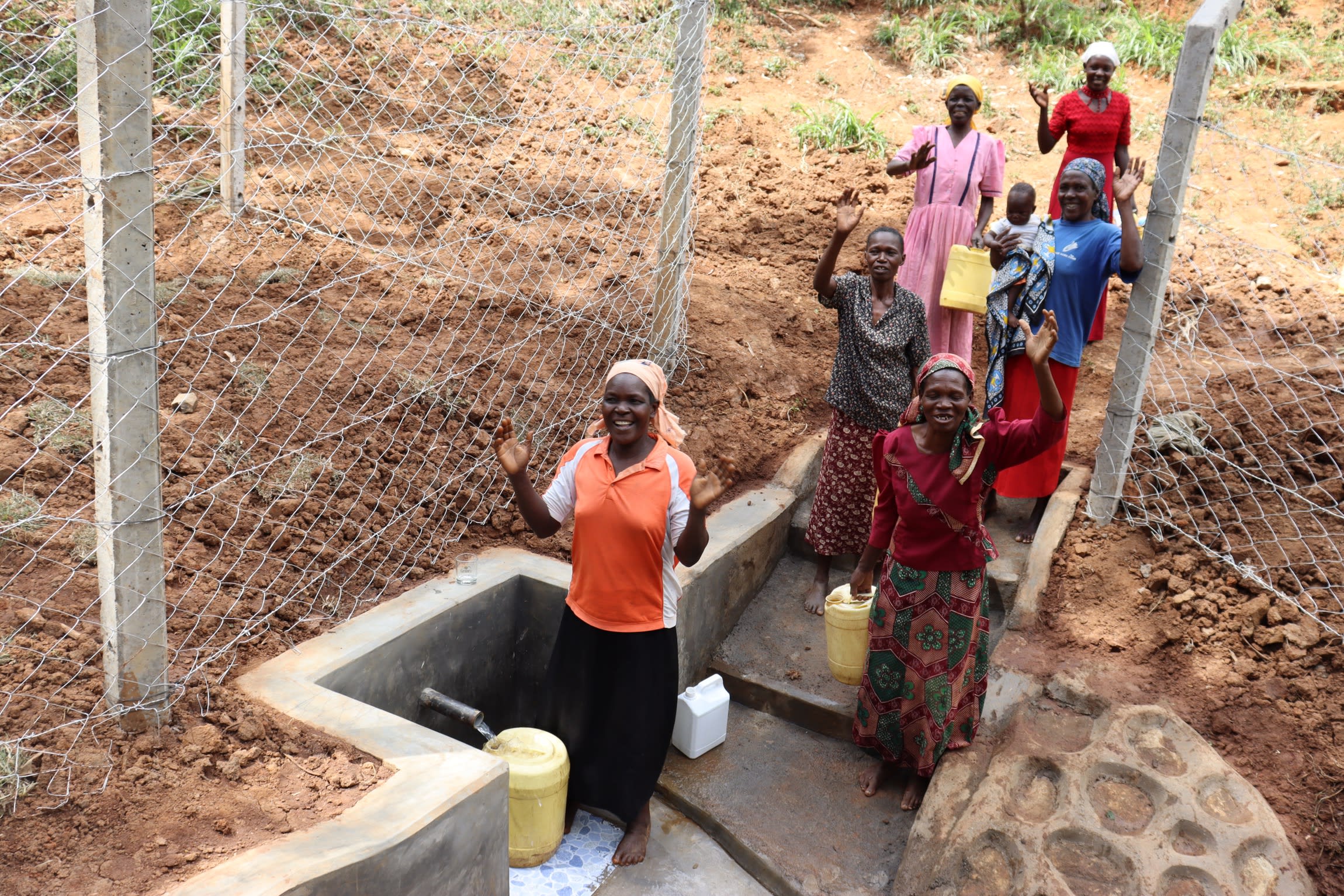
"When the spring was still under construction, I kept on wondering how water would [rise] up to the pipe level," said 65-year-old farmer Margaret Lukasile. "On the day backfilling was done, I had to be there to witness the magic. I was very excited to finally see water flowing. This has been my dream for many years. There will be no more waterborne and water-related diseases like typhoid and stomachache for my family and I."
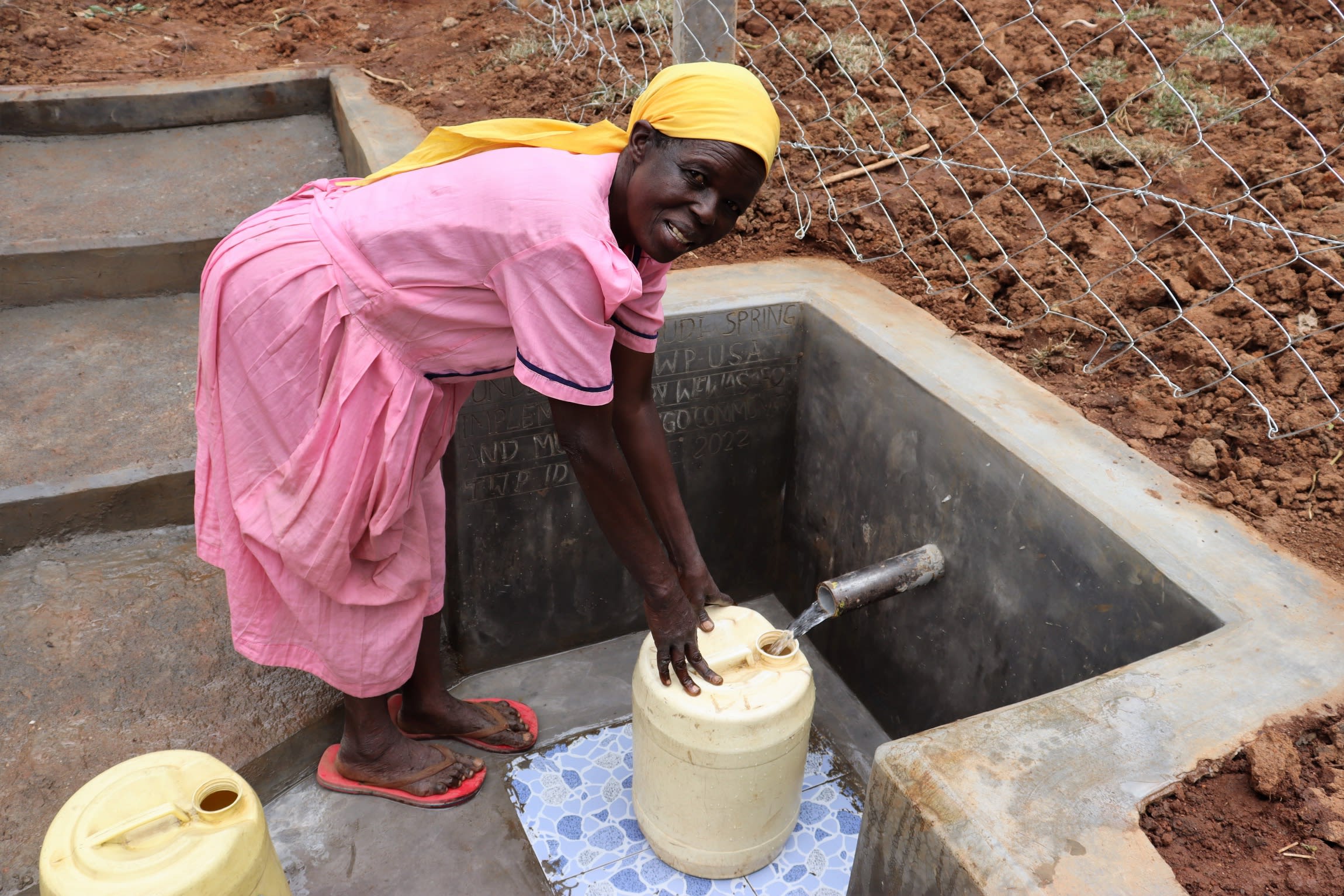
"Fetching water is easy and fast," Margaret continued. "I don't have to wake up early and go fetch water for the fear of not getting clean water for drinking. Water can be fetched at any time of the day and its cleanliness is guaranteed. Now I will have more time to attend to my ailing husband and also work in the farm."
Children were just as excited as adults about the new waterpoint.
"This water is very clean and safe for drinking," said nine-year-old Sammy A. "Before I could line up for [a] long [time] as I waited for my turn to fetch water, but now the jerrican is filled very fast through the installed pipe."

Sammy fills a glass.
"Accessing the spring is also easy since [the] stairs were put in place," Sammy continued. "With the current water point, I am able to assist my mum to fetch water, but still have time to do my homework and play, too."
Preparing for Spring Protection
Community members worked together to source and carry all locally available construction materials to the spring. These included bricks, sand, stones, and fencing poles. Some people also chiseled away at large rocks to break them down into gravel. Because people have to carry most items by hand, the material-collection process can take anywhere from a few weeks to months.
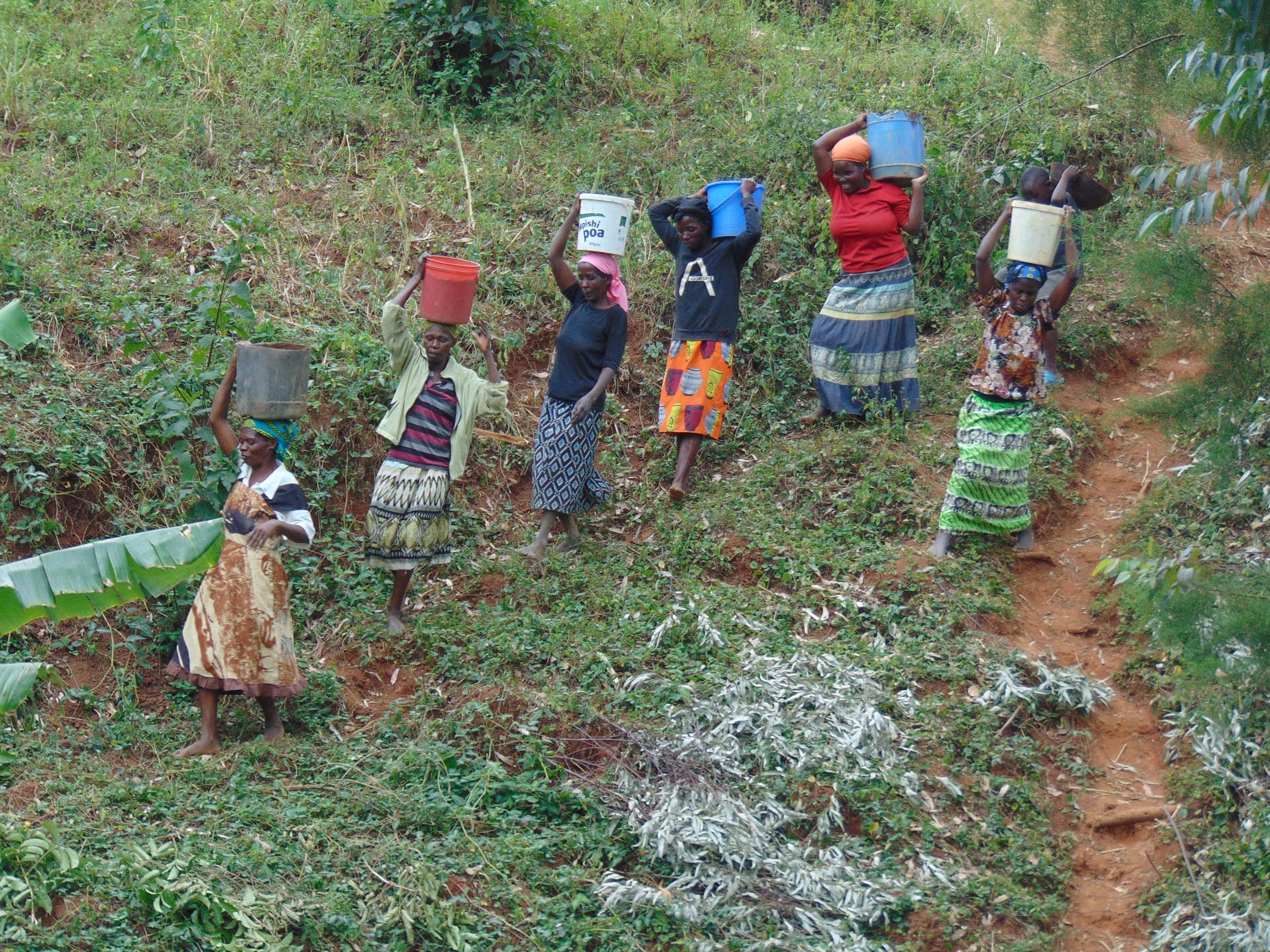
When the community was ready, we sent a lorry to deliver the remaining construction materials, including cement, plastic tarps, and hardware. Then, our construction artisan and field officers deployed to the spring to begin work. Individual households provided meals throughout each day to sustain the work team.
From Open Source to Protected Spring: A Step-by-Step Process
At last, it was time to dig in at the spring! Locals lent their strength to the artisans to help with the manual labor.
First, we cleared and excavated the spring area. Next, we dug a drainage channel below the spring and several runoff diversion channels above and around the spring. These help to divert surface contaminants away.
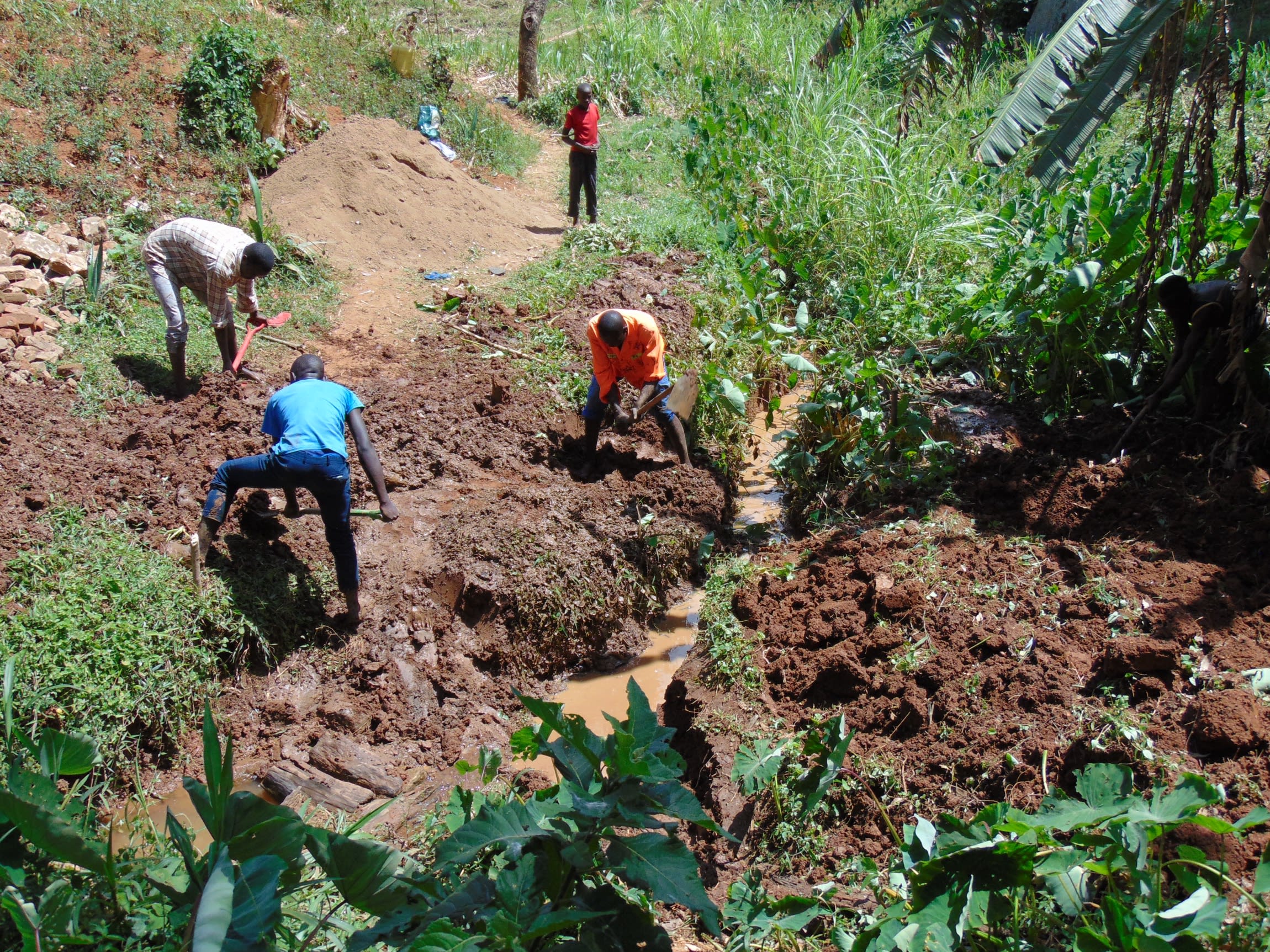
Community members assisted our artisans with excavation.
To ensure community members could still access water throughout the construction process, we also dug temporary channels from the spring's eye around the construction site. This allowed water to flow without disrupting community members' tasks or the construction work.
Excavation created space for setting the spring's foundation, made of thick plastic tarp, wire mesh, concrete, and waterproof cement. After establishing the base, we started brickwork to build the headwall, wing walls, and stairs.

Brickwork in progress.
Once the walls had grown tall enough, we began one of the most crucial steps: setting the discharge pipe. The discharge pipe needs to be positioned low enough in the headwall so the water level never rises above the spring's eye, yet high enough to allow room for the average jerrycan (a 20-liter container) to sit beneath the pipe without making contact.

If we place the discharge pipe too high above the spring's eye, backpressure could force water to emerge elsewhere. Too low, and community members would not be able to access the water easily. We embedded the pipe using clay (or mortar when clay is in short supply) and placed it at an incline to ensure water flows in the right direction.
In coordination with brickwork, we pitched stones on both sides of the spring's drainage channel. We then cemented and plastered each stone, forming the rub walls. These walls discourage people and animals from standing in that area, which could cause soil erosion and a clogged drainage area.
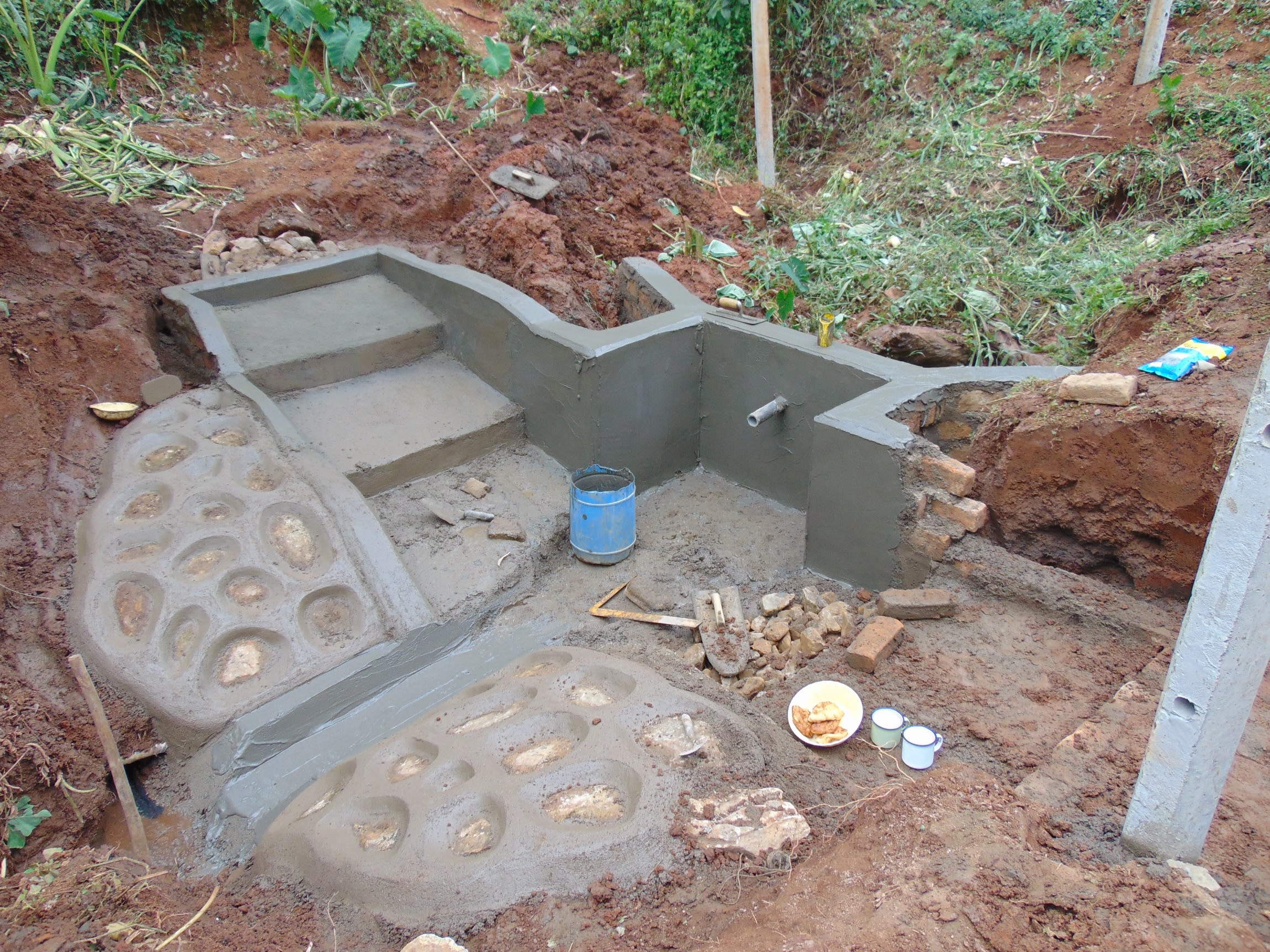
We then cemented and plastered both sides of the headwall and wing walls. These finishing layers reinforce the brickwork and prevent water in the reservoir from seeping through the walls. In turn, enough pressure builds in the reservoir box to push water out through the discharge pipe.
As the headwall and wing walls cured, we cemented and plastered the stairs and installed four tiles beneath the discharge pipe. The tiles protect the concrete from the falling water's erosive force while beautifying the spring and facilitating easy cleaning of the spring floor.
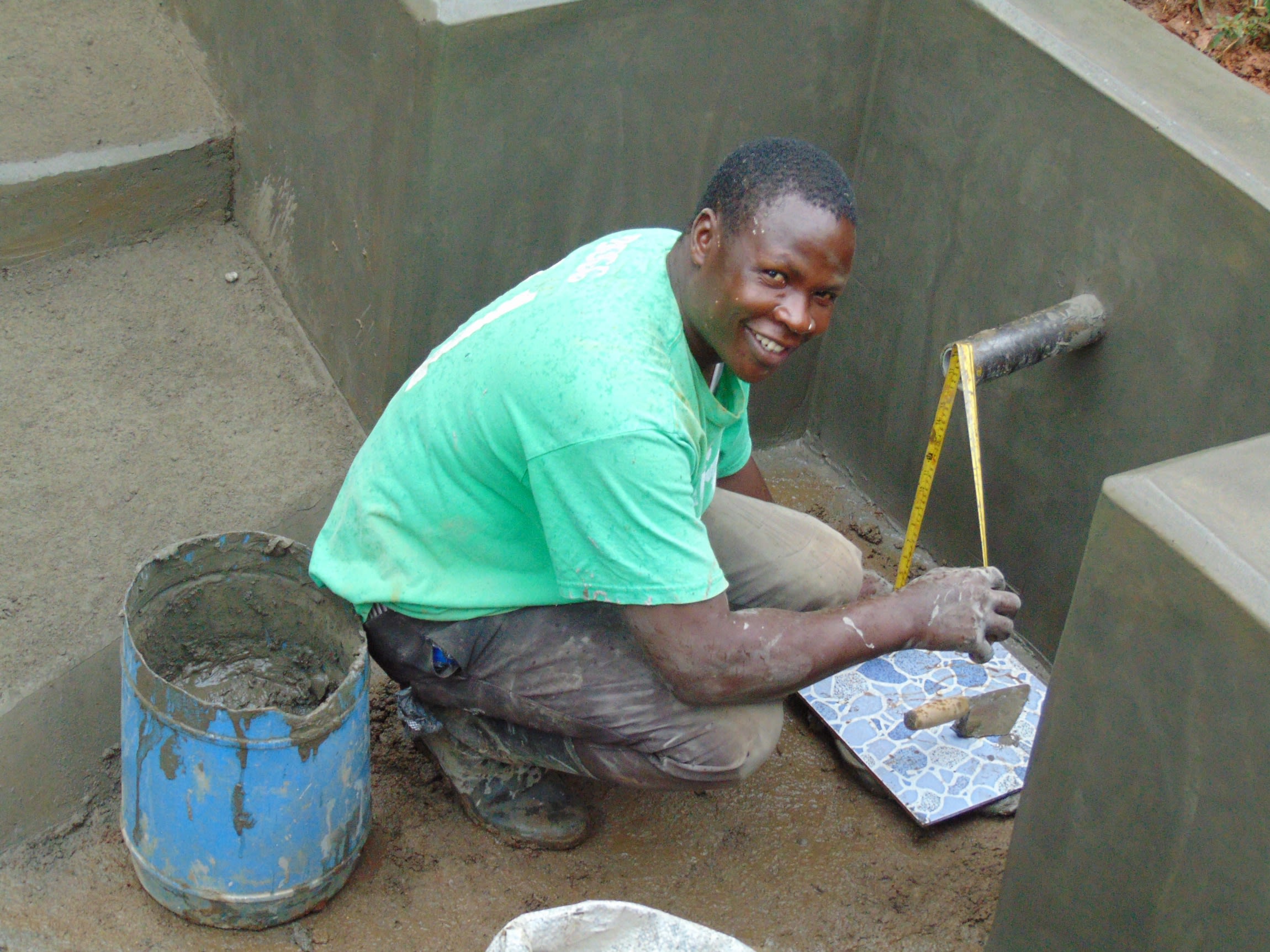
The final stage of construction is backfilling the reservoir box behind the discharge pipe. We cleared the collection box of any debris that may have fallen during construction. Then we redirected the temporary diversion channels back into the reservoir box, channeling water into this area for the first time. We closed off all of the other exits to start forcing water through the discharge pipe only.
We filled up the reservoir area with the large, clean stones community members had gathered, arranging them in layers like a well-fitting puzzle. We covered the rocks with a thick plastic tarp to minimize potential contamination sources, then piled enough dirt on top to compensate for future settling.
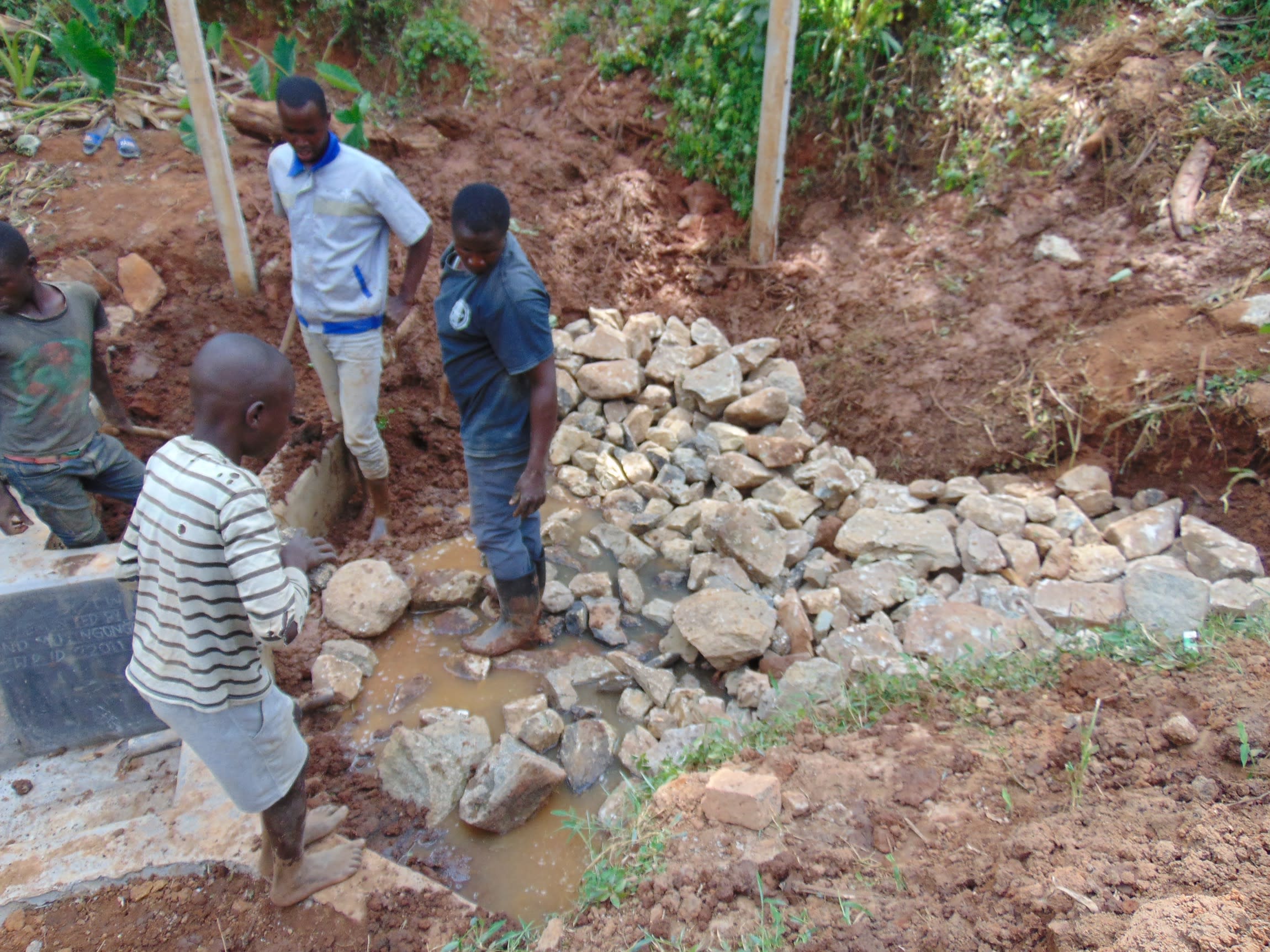
Community members transplanted grass onto the backfilled soil to help prevent erosion. Finally, the collection area was fenced to discourage any person or animal from walking on it. Compaction can lead to disturbances in the backfill layers and potentially compromise water quality.
The entire construction process took about two weeks of work and patience to allow the cement and plaster to finish curing. As soon as the spring was ready, people got the okay from our field officers to fetch water.
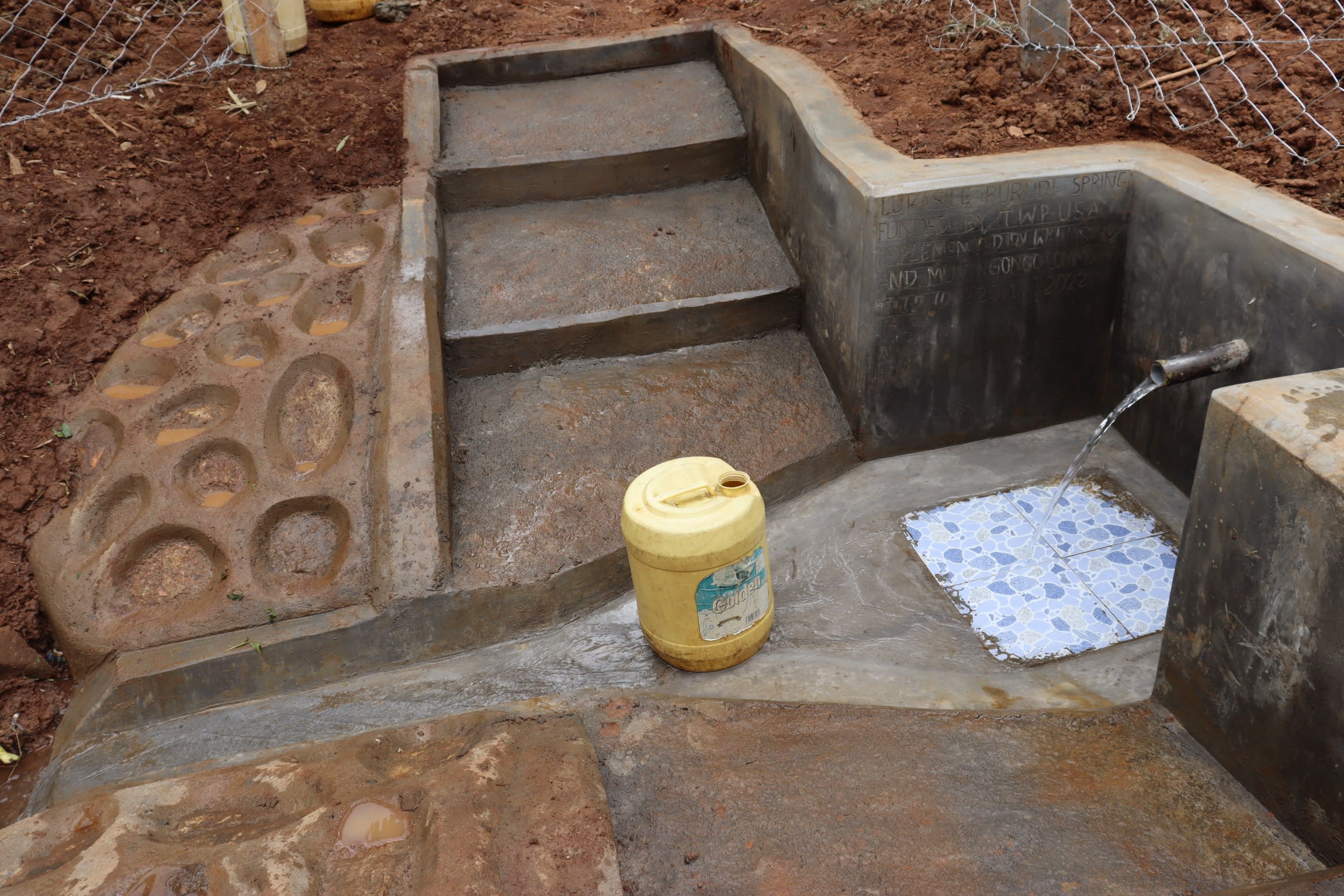
Finished waterpoint.
Training on Health, Hygiene, COVID-19, and More
Together with the community, we found their preferred date for training while considering other community calendar events, such as the agricultural season and social events. We requested a representative group of community members to attend training to relay the information learned to the rest of their family and friends.
When the day arrived, facilitators Christine, Samuel, and Oscar deployed to the site to lead the event. 21 people attended the training, including 15 women and six men. We held the training at our community contact Mr. Burudi's house.
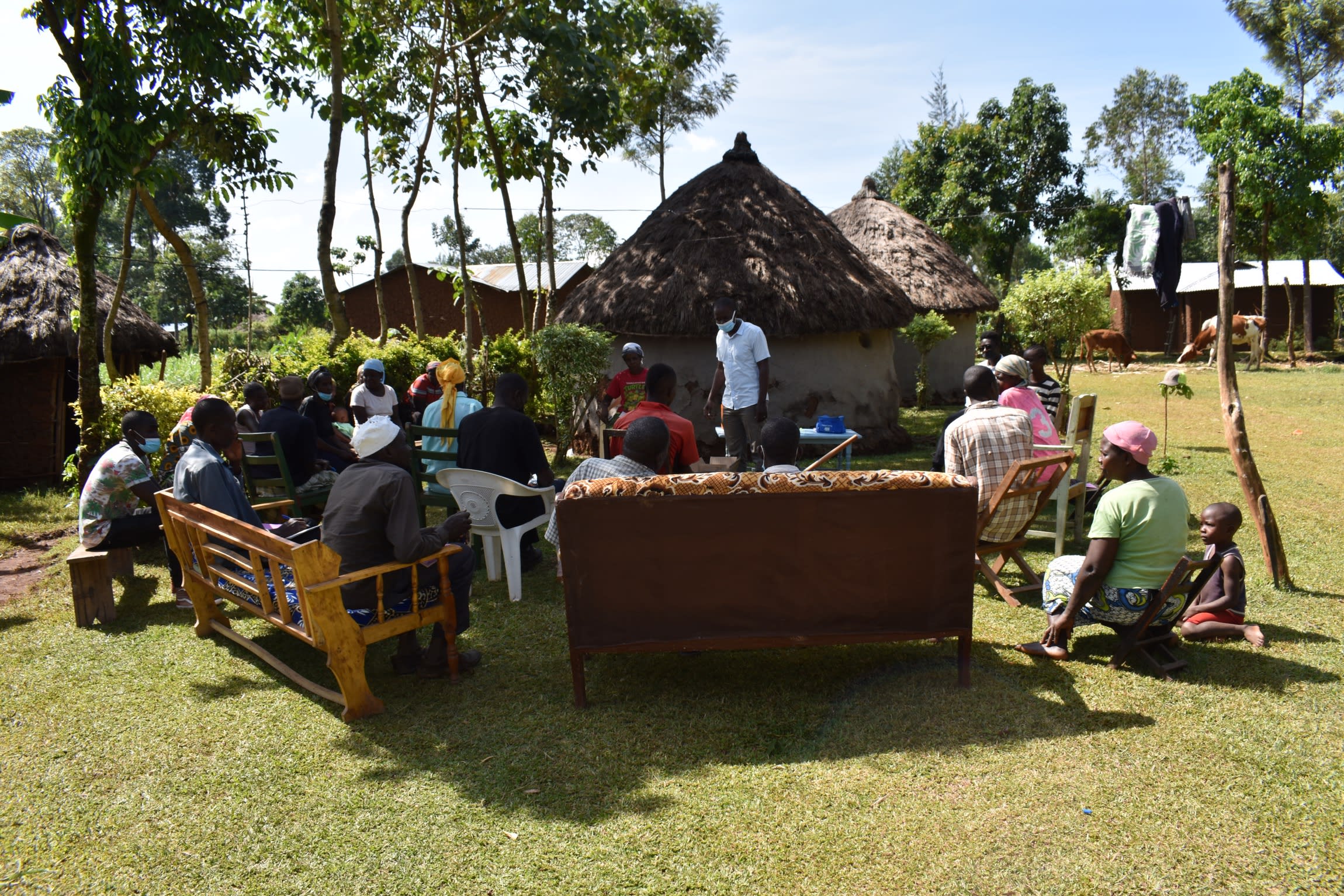
We covered several topics, including community participation in the project, leadership and governance, personal and environmental hygiene, water handling and treatment, spring maintenance, dental hygiene, the ten steps of handwashing, disease prevention, and how to make and use handwashing stations.
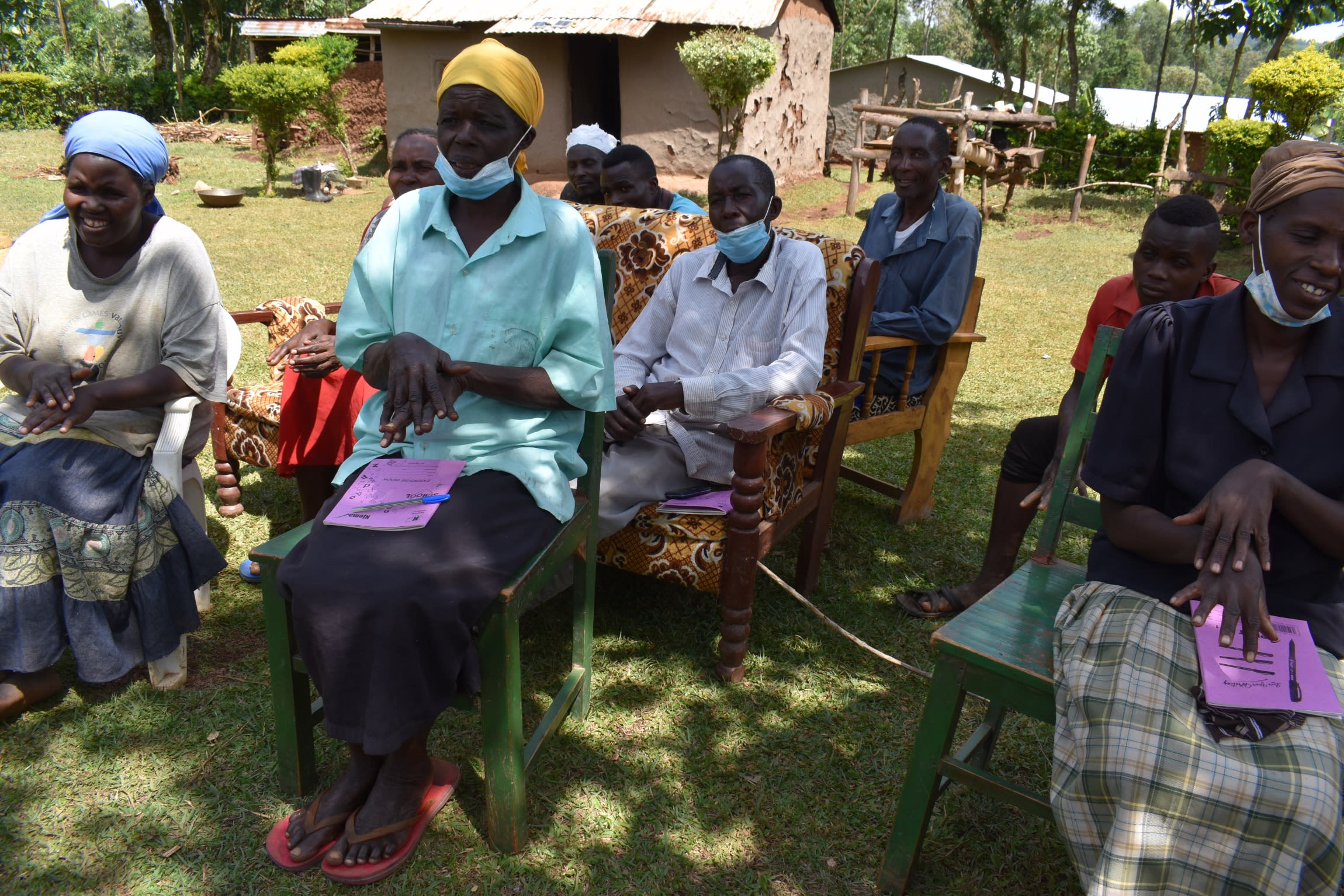
Community members watch the handwashing demonstration.
During the leadership and governance session, we held an election for the newly formed water user committee leaders, who will oversee the maintenance of the spring. We also brainstormed income-generating activities. Community members can now start a group savings account for any future minor repairs to the spring and a cooperative lending group, enabling them to develop small businesses.
One topic that got the community members talking was water handling and disinfection. We asked the participants how to handle water to keep it clean. One response that got the facilitators' attention was filtration. A woman said that she uses a piece of cloth to filter her drinking water, but she uses the same cloth for several days without cleaning it. She was urged to clean the cloth after each use.
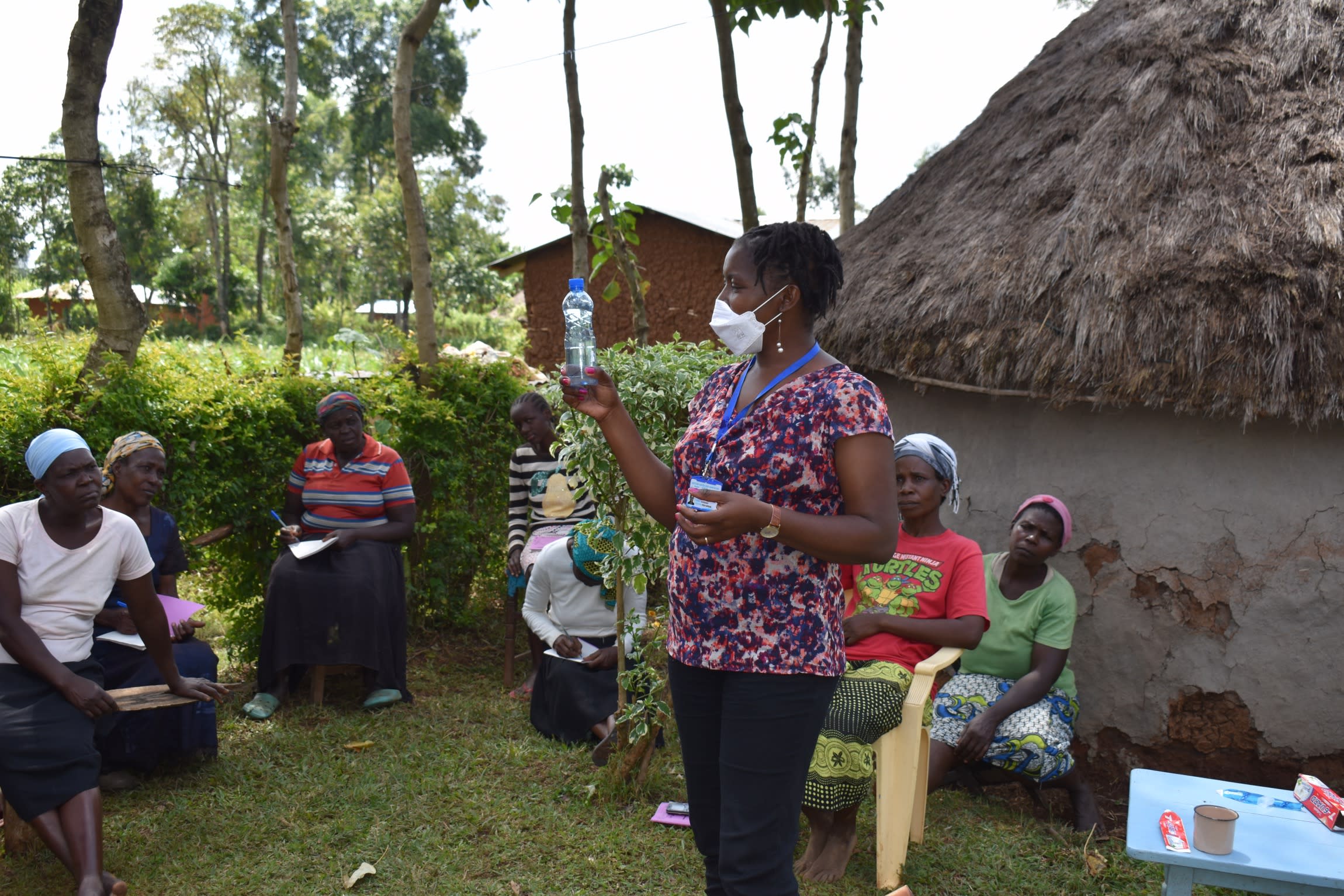
When an issue arises concerning the spring, the water user committee is equipped with the necessary skills to rectify the problem and ensure the water point works appropriately. However, if the issue is beyond their capabilities, they can contact our field officers to assist them. Also, we will continue to offer them unmatchable support as a part of our ongoing monitoring and maintenance program.
Thank you for making all of this possible!